Forging Steel – Get the best out of your material
Forging is your ideal choice of processing for products with the best mechanical properties. Thanks to the expertise of our partners, your product is shaped near to its final state during the forging process which guarantees a close-to-shape work piece. This ensures a high material usage and a lowered subsequent machining time. Near-net shape forgings can achieve up to 90% material usage, thus making forged goods a viable choice – economically and ecologically.
We are experts with over 50 years of experience with regards to forged goods. We can help you identify your needs and provide you with the right solutions for your product.
The forging process
Bringing steel into shape – the hot forging process
During the forging process, ingots or pre-forged bars are reheated to temperatures near two-thirds of the melting point of steel. This makes the material malleable and allows the forge masters to bring steel into shape.
This process is called thermo-plastic deformation, during which the underlying grain and texture of the material are reformed and lead to unrivalled mechanical properties. The deformation of the material leads to a fine grain structure, leading to a tough and ductile material response.
During the forging process, the material cools down and needs to be reheated, often multiple times for one part. Experienced forge masters can tell by the color of the glow whether the material is still hot enough for processing.
After forging, the material is subject to thermal treatment. This process ensures that the steel is in the right state – ferrite, austenite or martensite, and sometimes even multiple phases (for instance in Duplex who features austenite and ferrite) of them depending on the composition and the required properties. The latter depend on the sequence of heating and cooling and the rates of temperature change – Processes that the producers must master and that require special equipment for different cases and sizes.
Clearly, forging and thermal treatment are complex matters and require years of expertise and mastery to craft a high-quality product. That is why we only work with qualified and audited suppliers!
Some of our products
Standard and special-made flanges

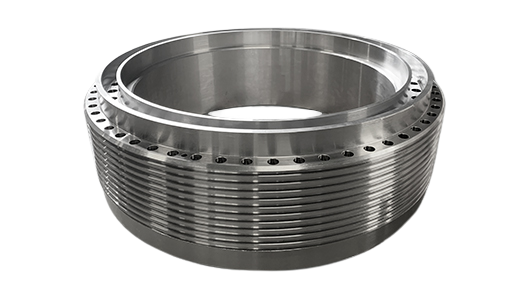
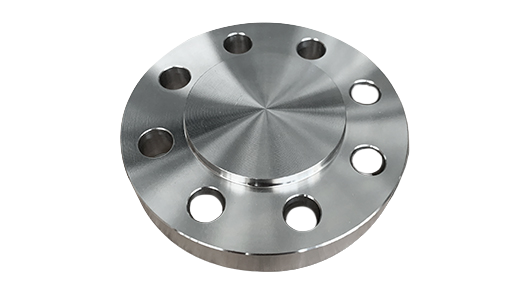
Crankshafts, shafts and bars – up to 100 tons
Thanks to our network of partners we are the right address for shafts and crankshafts, excentric machined shafts and many more in weight classes ranging from 500 kgs up to 80-100 metric tons in a variety of materials!

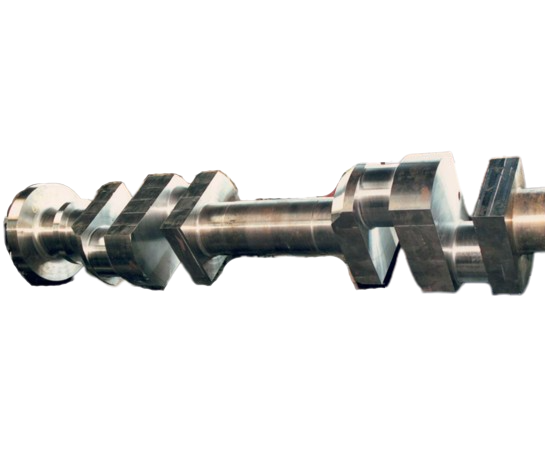
Blocks, discs, tubesheets
Our partners can manage discs up to ø2.2-2.5m and blocks up to 50 tons.

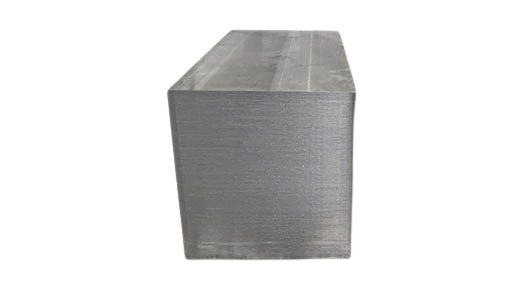
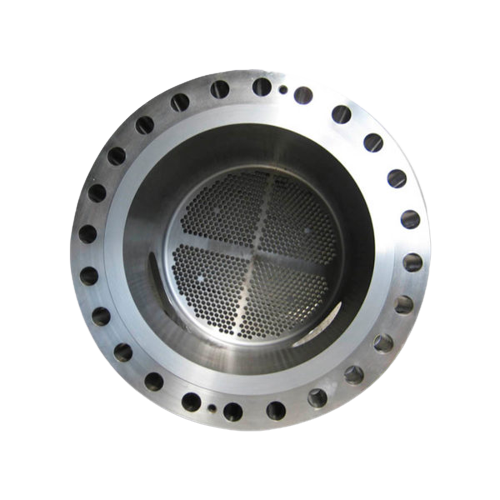
Rings, bushes and balls
With multiple ring rolling mills in our network we have the capability to produce hot-rolled rings and bushes starting from ø300mm up to ø6m and up to 2.5m height, we are convinced to have the right partner for your needs!

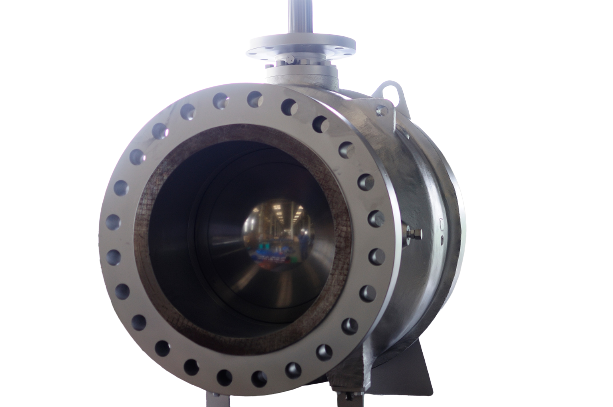
Some common materials we provide
Ferritic and martensitic steels | Stainless steels | Nickel alloys | Weldable fine-grain steel | Carbon steel |
Highly alloyed steels | Duplex | Superduplex | Titanium | Aluminium |
CONTACT US
For high-quality cast components that meet your specific requirements, contact INTEG. Our team of experts is ready to provide customized solutions and reliable support for your projects.